In practical situations, existing soil may not be suitable for construction work. Especially for sandy soil, the soil may not be dense enough. This makes sandy soil prone to large elastic settlements. Soil is then required to be densified to increase its unit weight. Consequently, the shear strength will improve. Sometimes, the topsoil needs to be removed and replaced with the soil of desirable characteristics.
In this article, we will discuss different methods and techniques generally used for the improvement of sandy soil.
However, in our previous article, we have discussed different aspects of sandy soil. If you are interested to learn more about sandy soil you can click and visit: What is Sandy Soil?- Uses of Sandy Soil. To learn more about sand visit our other article: What is sand? Composition, Color, and Types of Sand.
Sandy Soil Improvement Methods
The followings are the methods to improve sandy soil.
- Field Compaction
- Vibroflotation
- Blasting
- Cement Stabilization
- Fly Ash Stabilization
- Dynamic Compaction
- Jet Grouting
Field Compaction
Ordinary compaction in the field is done by rollers. The most commonly used rollers for sandy soil are the following.
- Smooth Wheel Roller
- Pneumatic Rubber-Tired Rollers
- Vibratory Rollers
A brief description of field compaction with these three types of rollers are given below.
Smooth Wheel Roller
It can create vertical vibrations during compaction. Smooth wheel rollers are suitable for proof-rolling subgrades and for finishing the construction of fills with sandy soils. They provide 100% coverage under the wheels. The contact pressure can be as high as 300 o 400 KN/m2. However, they do not produce a uniform weight of compaction when used on thick layers.
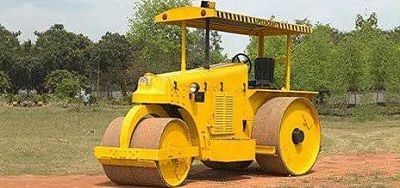
Pneumatic Rubber-Tired Rollers
They are better in many respects than smooth wheel rollers. Pneumatic rollers, which may weigh as much as 2000 KN consist of a heavily loaded wagon with several rows of tires. The tires are closely spaced- four to six in a row. The contact pressure under the tires may range up to 600 to 700 KN/m2 and they give about 70 to 80% coverage. Pneumatic rollers, which can be used for sandy soil compaction, produce a combination of pressure and kneading action.
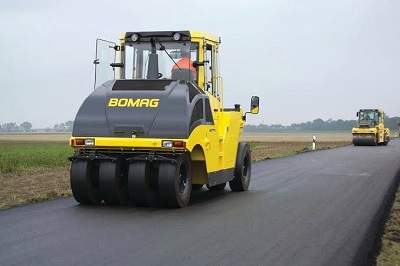
Vibratory Rollers
They are efficient in compacting granular soils. Vibrators can be attached to the smooth wheel, pneumatic rubber-tired or sheepsfoot rollers to send vibrations into the soil being compacted.
In general, compaction in the field depends on several factors. Such as the type of compactor, type of soil, moisture content, lift thickness, towing speed of the compactor, and the number of passes the roller makes.
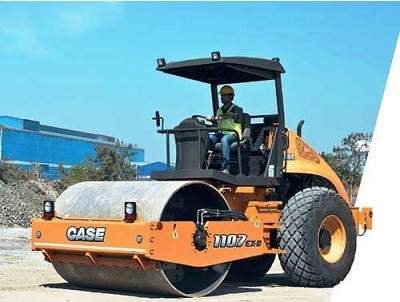
Vibroflotation
Vibroflotation is a technique developed for in situ densification of thick layers of loose granular soil deposits. The process involves the use of a vibroflot (called the vibrating unit). The device is about 2 m in length. This vibrating unit has an eccentric weight inside. It can develop a centrifugal force. The weight enables the unit to vibrate horizontally. Opening at the bottom and top of the unit are for water jets. The vibrating unit is attached to a follow-up pipe.
The entire compaction process can be divided into four steps.
Step 1. The jet at the bottom of the vibroflot is turned on. The vibroflot is lowered into the ground.
Step 2. The water jet creates a quick condition in the soil. Which allows the vibrating unit to sink.
Step 3. Granular material is poured into the top of the hole. The water from the lower jet is transferred to the jet at the top of the vibrating unit. This water carries the granular material down the hole.
Step 4. The vibrating unit gradually raised in about 0.3 m lifts. It is held vibrating for about 30 seconds at a time. This process compacts the soil to the desired unit weight.
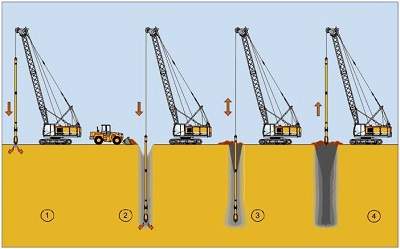
The success of the densification of in situ soil depends on several factors, the most important of which are the grain size distribution of the soil and the nature of the backfill used to fill the holes during the withdrawal period of the vibroflot.
Blasting
Blasting is a technique that has been used successfully in many projects for the densification of granular soils. The general soil grain sizes suitable for compaction by blasting are the same as those for compaction by vibroflotation.
The process involves the detonation of explosive charges such as 60% dynamite at a certain depth below the ground surface in saturated soil. The lateral spacing of the charges varies from about 3 to 9 m. Three to five successful detonations are usually necessary to achieve the desired compaction.
Compaction (up to a relative density of about 80%) up to a depth of about 18 m over a large area can easily be achieved by using this process. Usually, the explosive charges are placed at a depth of about two-thirds of the thickness of the soil layer desired to be compacted.
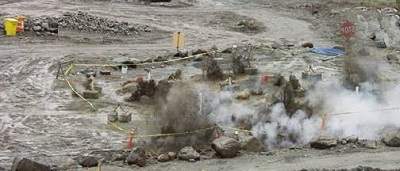
Read more: Blasting - A Technique for Soil Improvement
Cement Stabilization
Cement is being increasingly used as a stabilizing material for soil. It is particularly used in the construction of highways and earth dams. Cement can be used to stabilize both sandy and clayey soils. As in the case of lime, cement helps decrease the liquid limit and increase the plasticity index and workability of clayey soils. Cement stabilization is effective for clayey soils when the liquid limit is less than 45 to 50 and the plasticity index is less than about 25.
Like lime, cement helps increase the strength of soils. The strength increases with the curing time.
Granular soils and clayey soils with low plasticity obviously are most suitable for cement stabilization. Calcium clays are more easily stabilized by the addition of cement. On the other hand, Sodium and hydrogen clays, which are expansive in nature, respond better to lime stabilization. For these reasons, proper care should be given in the selection of the stabilizing material. For field compaction, the proper amount of cement can be mixed with soil either at the site or at a mixing plant. If the latter approach is adopted, the mixture can then be carried to the site. The soil is compacted to the required unit weight with a predetermined amount of water.
Similar to lime injection, cement slurry made of Portland cement and water can be used for pressure grouting of poor soils under the foundations of buildings and other structures. The water-cement ratio could be of 0.5:5. Grouting decreases the hydraulic conductivity of soils. It increases their strength and load-bearing capacity. For the design of low-frequency machine foundations subjected to vibrating forces, stiffening the foundation soil by grouting and thereby increasing the resonant frequency is sometimes necessary.
Fly Ash Stabilization
Fly ash is a by-product of the pulverized coal combustion process usually associated with electric power-generating plants. It is fine-grained dust. It is composed primarily of silica, alumina, and various oxides and alkalis. Fly ash is pozzolanic in nature. It can react with hydrated lime to produce cementitious products. For that reason, lime–fly-ash mixtures can be used to stabilize highway bases and subbases. Effective mixes can be prepared with 10 to 35% fly ash and 2 to 10% lime. Soil–lime–fly-ash mixes are compacted under controlled conditions, with proper amounts of moisture to obtain stabilized soil layers.
Dynamic Compaction
Dynamic compaction is a technique that is beginning to gain popularity in the United States for the densification of granular soil deposits. The process primarily involves dropping a heavyweight repeatedly on the ground at regular intervals. The weight of the hammer used varies from 8 to 35 metric tons, and the height of the hammer drop varies between 7.5 and 30.5 m.
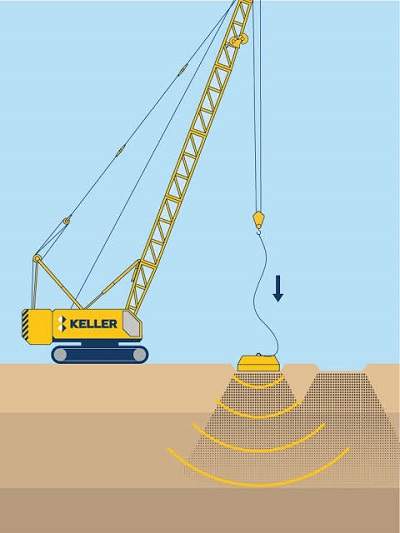
The stress waves generated by the hammer drops help in the densification. The degree of compaction achieved depends on
- The weight of the hammer
- The height of the drop
- The spacing of the locations at which the hammer is dropped
Jet Grouting
Jet grouting is a soil stabilization process whereby a cement slurry is injected into the soil at a high velocity to form a soil–concrete matrix.
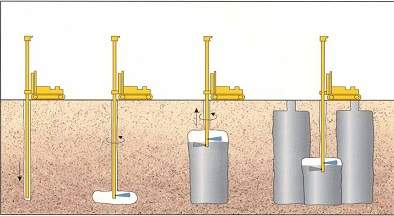
Three basic systems of jet grouting have been developed—single, double, and triple rod systems. In all cases, hydraulic rotary drilling is used to reach the design
depth at which the soil has to be stabilized.
The effectiveness of jet grouting is very much influenced by the nature of erodibility of soil. Gravelly soil and clean sand are highly erodible, whereas highly plastic clays are difficult to erode.
Sand Articles
- What is sand? Composition, Color, and Types of Sand
- Uses of sand
- What is Sandy Soil?- Uses of Sandy Soil
- How to Improve Sandy Soil
- What is the Bulking of Sand? - Significance & Test Steps
- What is Silica Sand? Sources & Uses of Silica Sand
- Types of Silica Sand
- The Health Risks of Silica Sand
- Bulk Density of Sand
- Specific Gravity of Sand
- Sand Unit Weight
References
- Das, B. M. (2011). Principles of foundation engineering(7th ed.). Boston, MA: Cengage Learning.
- Bowles, J. E. (1984). Physical and geotechnical properties of soils(2nd ed.). New York: McGraw-Hill.
- https://www.designingbuildings.co.uk/wiki/Types_of_roller
- https://www.forconstructionpros.com/asphalt/article/10616882/clearing-the-air-about-pneumatic-rollers
- https://www.indiamart.com/proddetail/case-double-drum-vibratory-roller-4965269662.html
- https://www.geoengineer.org/education/web-class-projects/cee-542-soil-site-improve-winter-2014/assignments/vibroflotation
- https://civildigital.com/blasting-technique-for-ground-improvement/
- https://www.keller.co.uk/expertise/techniques/dynamic-compaction
- https://research.engineering.ucdavis.edu/gpa/ground-improvement/jet-grouting/